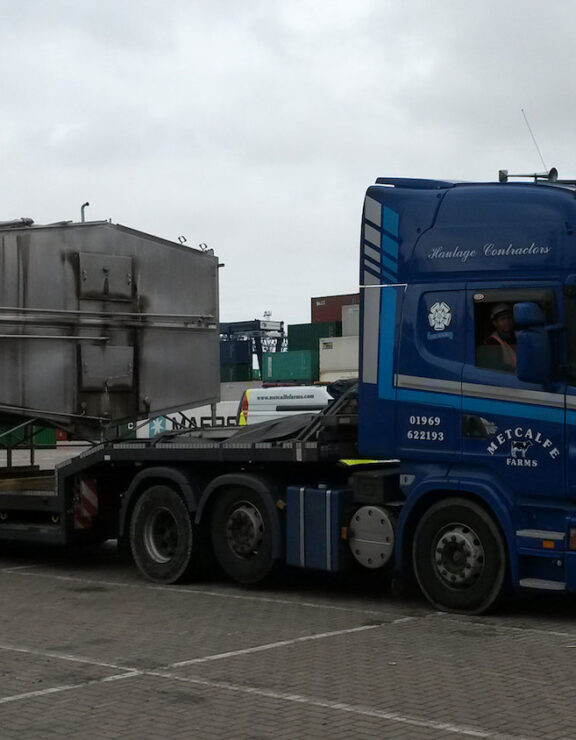
Plant Relocation
Overview
When Hemisphere were contacted at the 11th hour by a new client whose shipment was already underway, our project managers quickly stepped in and were able to assess the client’s requirements and find a suitable solution.
Unfortunately, the client had been let down when another party were no longer able to offer a workable solution. Within hours, we presented a tailor-made and fully comprehensive transport solution, which not only met the shipper and consignee’s needs, but was also substantially under our client’s initial budget for the shipment.
Within the same day, applications had been made to the UK Highways Agency for the permits required to move the biggest pieces of the production plant.
Delivery
Our project manager quickly realised that the most economical solution was to relocate the heavy-duty, heat-treated packing timbers, which would eventually be used in the sea freight packing. A truck was dispatched the same day from Felixstowe to the factory site, so that the timbers were available to support the plant when it was loaded to our trucks.
Even split into two sections, each half of the main machine was still over 8 metres in length, nearly 5 metres wide and almost 4 metres high. Escort vehicles were required at both the front and rear of the convoy, which had to travel over 300 miles, partly through the small winding roads of the Snowdonia mountain range, to the Port of Felixstowe.
All of which was filmed by a TV production company following our trusted trucking partner for the award-winning documentary TV series – Supertruckers.
On arrival of the cargo at Felixstowe port, our personnel were on hand to witness and oversee the lifting and loading operation from truck to the flat rack shipping containers, as per the loading plan that we had already provided to the loaders.
Our thoughts
Results
The final piece of cargo to arrive was a large steel gantry section, to be loaded onto a flat rack container. On arrival it was discovered that the factory dismantlers had placed a large amount of loose steel pipework inside the open gantry frame.
Our project manager inspected the cargo in conjunction with the loaders and the shipping line appointed cargo surveyor, and were able to agree the quickest and safest resolution to this problem, was to decant all the loose pipework to a further 40ft dry container where it could be safely contained and with minimal additional costs to the client.
Within 1 week of receiving the initial client call, all cargo was transported to port and loaded into the required containers, ready for export shipment. The cargo arrived at the final destination port in Izmir, Turkey, on time and under our client’s budget.
We always take pride in our work, and a successfully completed job and a happy customer, makes it even more worthwhile.